Big Machines of HQ: The Beluga
When we announced our new HQ in Butner, North Carolina, the best word we had to describe our new space was BIG. And guess what? Using that space to create Nuggets requires some equally gigantic, ginormous, gobsmackingly gargantuan — in other words, big — machines. In this series, we’re going behind-the-scenes to learn more about the Big Machines of Nugget HQ. Today’s feature: the roll pack machine we lovingly call The Beluga.
Meet our White Whale
The roll pack machines that we now use at HQ are a far cry from where we started in 2014, in a former tobacco warehouse in Durham, NC. Back then, we’d place a Nugget into a bag by hand, then use a forklift with three thousand pounds of bricks (yes, you read that right!) to squish down the Nugget, vacuum out the extra air, and seal the bag. Once the Nugget was wrestled into submission, we’d slip it into a cardboard tube (not as graceful as it sounds), and send it on its way. All in all, it could take more than 10 minutes to make and ship a single Nugget.
Back in those days, the Nugget team would dream about one day getting their hands on a roll pack machine, which would dramatically change how many Nuggets could be made and shipped in a day — and get rid of all that squishing and bagging by hand! Over time, the roll pack machine became known as The Beluga — the mythical white whale that we aspired to and yearned for.
These days, we’re the proud owners of not just one, but five Belugas, and we’re pretty happy about that! These machines are pivotal for doing the squishing and rolling up of Nuggets that we used to do by hand (and by forklift). Typically, these machines are used for prepping mattresses for shipment, but we’ve modified ours to perfectly fit Nuggets. These machines are powered by electricity, air pressure pneumatics, and hydraulics, and include monitors to control the machines, sensors to detect Nuggets within the machine, and safety interlocks on all the doors. The Beluga is definitely one of the more complicated Big Machines at HQ!
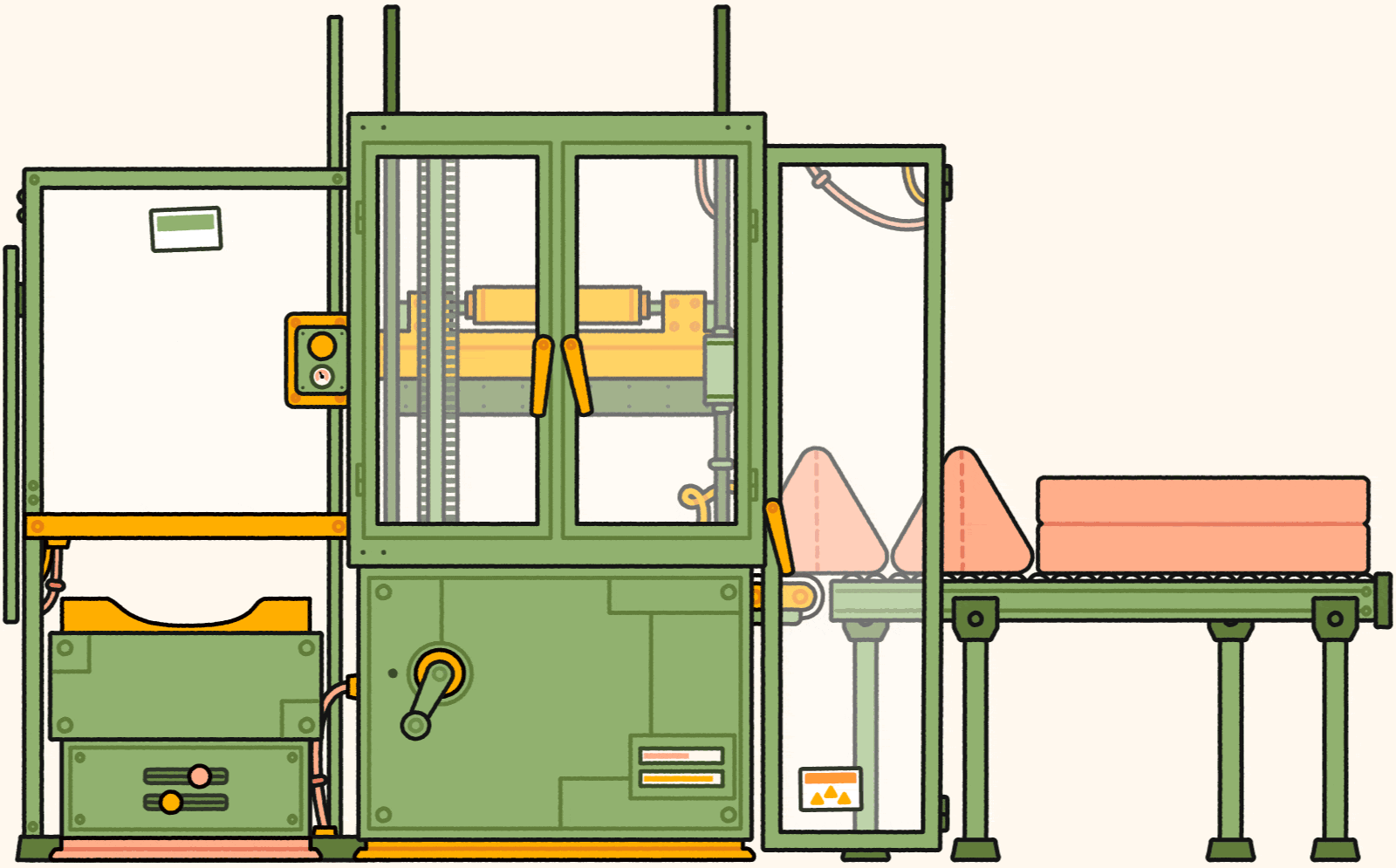
Baby Beluga, in Nugget HQ...
Fully dressed Nuggets — that is, with Nugget Covers fully on and zipped — come down the line and are pulled two at a time to a Beluga. A Production Team member checks the final product — pillow, pillow, cushion, base — lines it up just so, gently pushes it on its way into a Beluga, and lets the machine do the rest.
As soon as the Nugget enters a Beluga, the plastic wrapping rolls over and around, ensuring a tight squeeze for the whole trip to the Nugget’s future home. A heat bar lowers to cut just the right amount of plastic for each Nugget. The compressed Nugget is pushed and rolled into a cage at the end of the conveyor, in a reverse sushi roll technique. How much weight is needed to make Nuggets burritos ready for shipment? Um, a good bit... a Beluga pushes down with about the weight of an African forest elephant: 6,000 pounds!
Once the Nugget is fully wrapped and compressed, another heat bar lowers to weld the plastic seam tight. We use high grade, single source plastic that keeps Nuggets clean and can be efficiently recycled. After a quick cool down, the roll cage opens up, sensors check to make sure the coast is clear, and the fully wrapped Nugget is popped out onto the conveyor belt.
Anyone remember what happens next? Ding ding ding! The conveyor belt carries the perfectly wrapped Nugget up, up, and away to the burrito dropper.
We’re so grateful for our Belugas, the roll pack machines that make the Nugget shipping world go ‘round. They make it possible for us to prepare a Nugget every eight seconds — a mind-boggling number, especially when we think about how much we’ve grown as a company these past seven years.
There are a lot of moving parts to making, packaging, and shipping Nuggets from HQ to homes across the country. Our Big Machines series walks you through how we’ve been able to scale up our production since moving to Nugget’s new HQ in Butner. Find past editions of Big Machines on our blog under Our Factory!